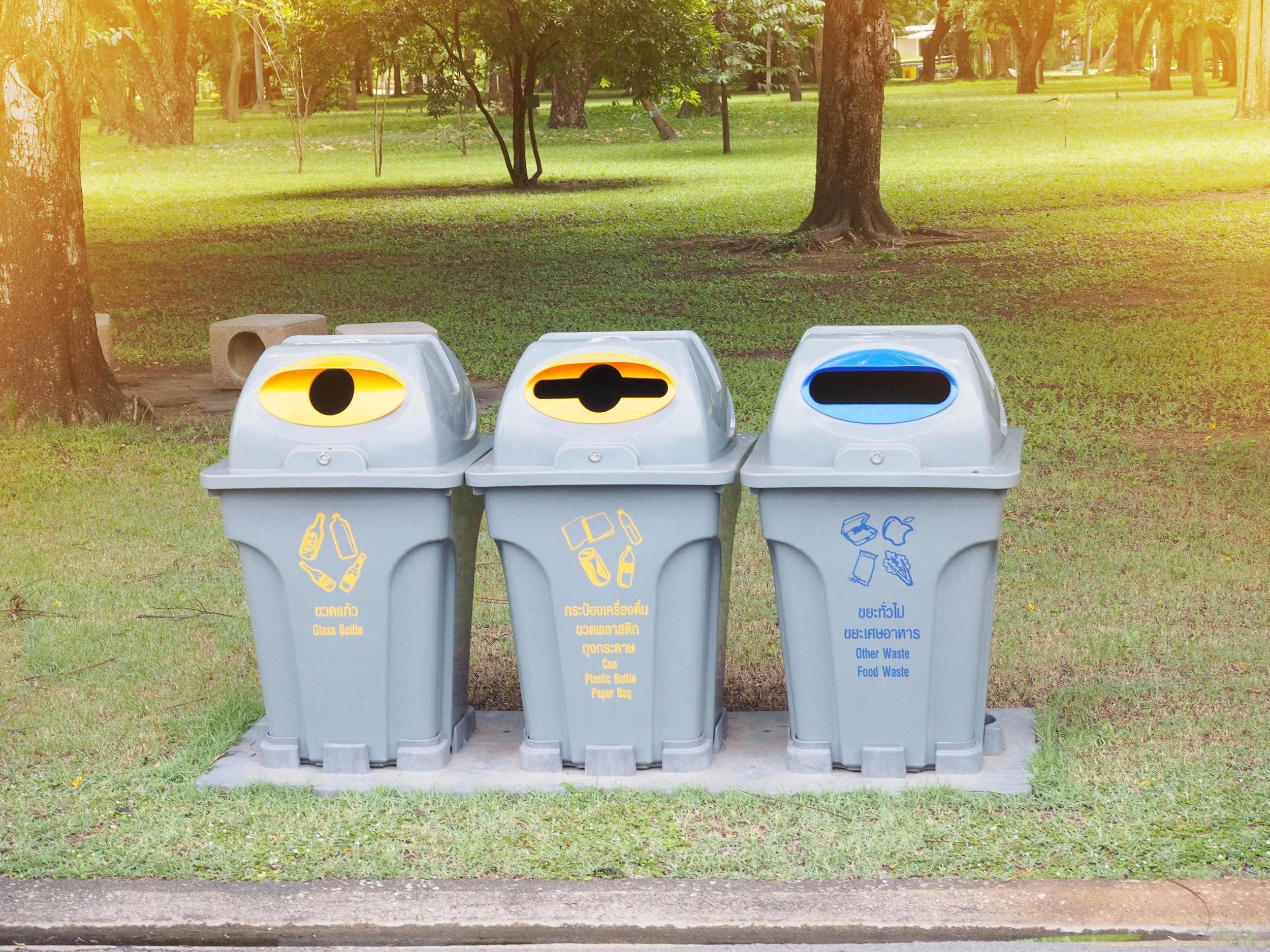
ENVAC
Service Work Order Solution Increases Efficiency for Vacuum Waste Collection Company
Envac AB is one of the leading environmental technology companies in Sweden and the global leader in the vacuum waste collection industry. In 1961, Envac invented the vacuum waste system that is in operation all over the world. Today, they design and install turnkey automated waste collection systems for residential and commercial developments, hospitals, airports, industrial kitchens and town centers. Vacuum waste collection transports waste at high speed through underground tubes to a collection station where it is compacted and sealed in containers.
Challenge
With a vast expanse of underground vacuum systems to service, Envac needed to close the gap between their workers in the field and the data located in their Oracle EnterpriseOne system. Envac’s field service workers travel to job sites to perform scheduled maintenance and break/fixes on underground systems using parts available on their trucks. Workers were responsible for manually keeping track of parts used, work performed and the time spent performing it.
The manual, paper-based processes slowed down every aspect of Envac’s workflow. Charlotte Anderson, Customer Success Manager, Envac described the labor-intensive manual procedures, “We texted out an SMS to the technicians with their daily task, which they wrote down on a piece of paper. They added to the paper what they did as a result of the job and the office used that to add the hours and measurements of the job into the system for invoicing.”
All of this slowed down Envac’s invoicing system, causing them to waste valuable time on manual organization.
Solution
Envac chose Cloud Inventory® to implement a mobile-first Work Order Solution with seamless integration to their current Oracle EnterpriseOne system. Using Cloud Inventory’s work order apps allows Envac’s maintenance engineers to visit waste sites and perform maintenance and services while they are underground, in disconnected environments. The Cloud Inventory solution allows workers to view existing work orders, make changes, add notes, create new work orders, view previous work order history at a specific site, view inventory, and allocate available inventory to an existing work order, all from their handheld device.
Once workers return to a connected environment, the data they collected while offline in the field syncs to Envac’s system of record, making the data available to the back-end office for rapid invoicing and payment.
Results
With Cloud Inventory’s mobile-first Work Order Solution, Envac workers are now able to view inventory available outside of their trucks. Digitizing their processes with mobile apps puts information into the hands of the workers on site. The app integration to Envac’s Oracle system ensures that workers have access to stored data when and where they need it most. Workers in the field can manage their own work orders and time entry, by clocking in and out on their mobile device and associating their time with a specific work order.
The availability of data reduced the strain on Envac’s internal resources by speeding work orders that were ready for billing. Work orders can now be processed within a day of services being performed, so invoices are ready to go out the next day. Cloud Inventory’s solution not only boosted Envac’s efficiency and accuracy, but also freed up their cash flow by allowing them to bill and receive payments faster.
Industry
Manufacturing & Distribution
ERP: JD Enterprise One
Highlights
Streamlined invoicing increased on-time payments and overall cash flow
Connected maintenance staff in the field for inventory visibility
Reduced strain on resources led to improved efficiency and accuracy
Jobs are being sent out with the help of Cloud Inventory, the technicians accept the jobs with the help of Cloud Inventory and… it’s off to invoicing straight away.