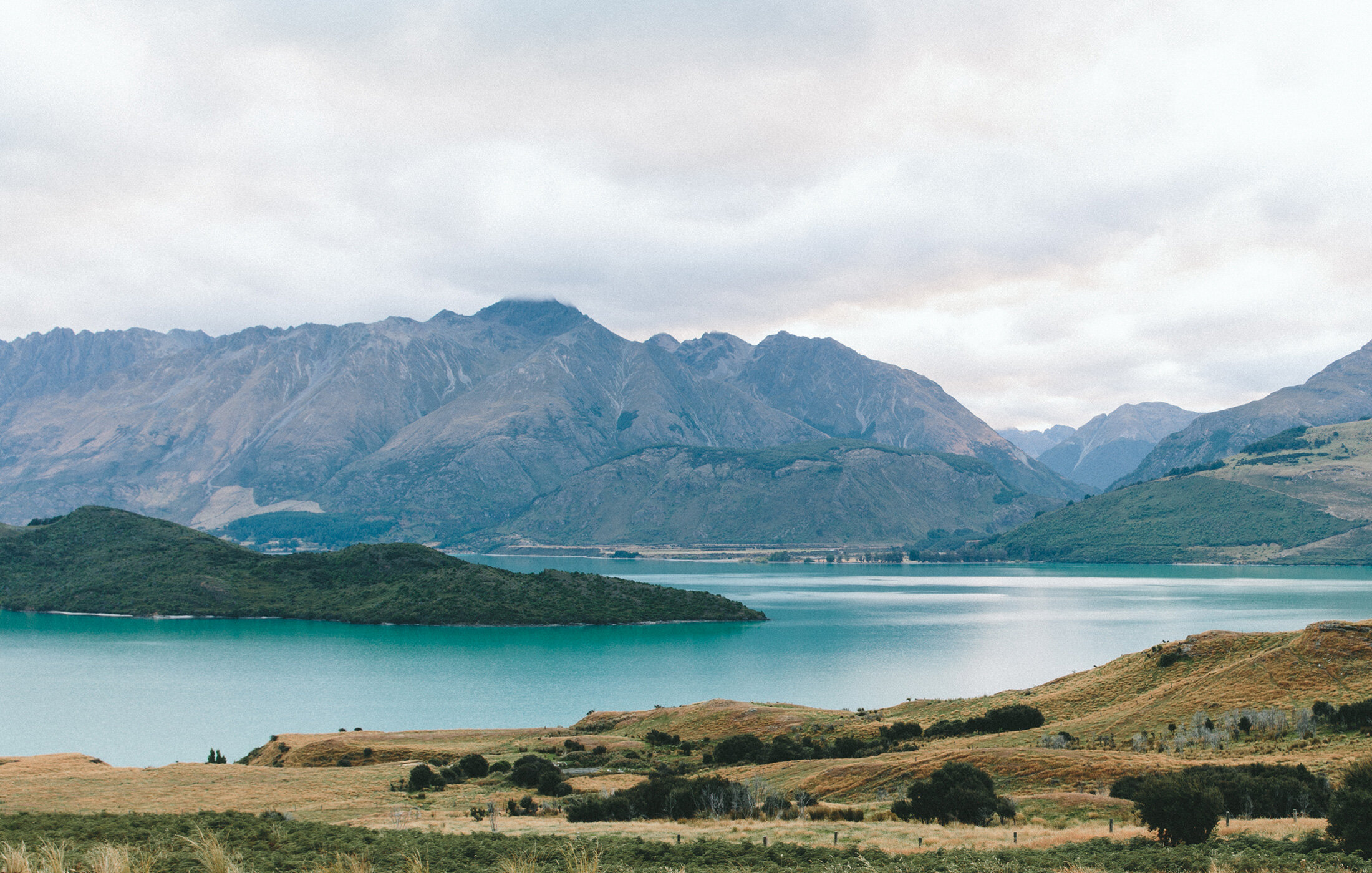
IWA
Wine Accessories Maker Boosts Warehouse Productivity and Speeds Order Fulfillment With Pick and Ship Apps
For more than a decade, International Wine Accessories (IWA), headquartered in Petaluma, California, has delighted its customers by offering a wide variety of wine accessories, dispensers and cellar equipment. As their slogan proudly says, they truly have “everything for the wine lover.” IWA’s extensive ecommerce selection includes everything from stemware to wine openers to custom wine cellars. They needed a solution to help them manage this inventory, fulfill orders quickly and accurately, integrate with machine-to-machine processes, and to provide their customers with the best experience possible.
Challenge
IWA’s pick and ship processes were largely manual, resulting in inefficient product picking and slow order shipments. As demand and product volume continued to grow, IWA could no longer utilize a single person per warehouse to pick and ship product orders manually, especially during holiday season when orders surge. IWA needed a way to scale their existing infrastructure to help them move more product through the system to meet demand.
With NetSuite already in place, IWA sought a solution to seamlessly integrate with their existing ERP implementation and extend their machine-to-machine capabilities. They didn’t want to invest in additional hardware and were looking for a simple, intuitive software solution that didn’t require a lot of IT maintenance. Additionally, they wanted real-time visibility into their inventory and the ability to select the most cost-effective shipping rate for each order.
Solution
With the Cloud Inventory® Picking App, IWA’s picking processes became much more organized and efficient. Access to picking lists became much faster through the handheld device allowing workers to scan and process 15 to 20 orders at a time.
The app also generated the most efficient pick route in the warehouse to accelerate pick time and order fulfillment. Streamlining this process has eliminated time consuming manual steps helping them to process orders faster and optimizing their warehouse productivity overall.
IWA also integrated Cloud Inventory’s Shipping App into their NetSuite system to simplify shipping options. Previously, employees navigated through several screens and performed multiple keystrokes to complete the shipping process for each individual order. In their new process, the Cloud Inventory app is integrated into their NetSuite ERP so they can access shipping rates for multiple carriers in real time. Default box size and default weight is automatically generated by the system for each order allowing a single keystroke to complete most orders instead of three or four. This also enables employees to choose the least expensive shipping method for every single order, resulting in significant cost savings for IWA.
Results
With Cloud Inventory’s pick and ship applications, IWA’s warehouse is running significantly smoother and faster than it was just a few months ago. With a 20% year over year improvement in orders processed since implementation, IWA is confident that they can handle the ebbs and flows of seasonal orders as well as scale meet the challenges ahead as their business grows.
Cloud Inventory’s pick and ship applications have streamlined and sped the order fulfillment process for IWA without increasing head count. Instead, they have enabled their existing staff to process more orders in a shorter amount of time with the utmost accuracy.
“It’s speedy, which is incredibly important when we’re doing hundreds of orders a day,” said Bruce Kirsten, IWA co-owner. “It’s cost effective because we had an idea which method was the most cost effective, but we never knew for sure. And now we see the dollars and cents there.”
With their pick and ship processes streamlined and efficient, IWA is moving more orders than ever before and is looking to expand these efficiencies throughout their warehouse operations.
Industry
Food & Beverage
ERP: Oracle NetSuite
Highlights
Expanded visibility into warehouse inventory
Established more efficient picking processes by eliminating manual processes
Generated picking orders in a more organized way to boost productivity in the warehouse
Enabled employees to select the most cost-effective shipping options for every order
Whatever it is, the way you tell your story online can make all the difference.